Your session is about to timeout due to inactivity. Click OK to extend your time for an additional 120 minutes.
Pallet racking is the typical materials handling system used in warehouses and many other storage facilities, but there’s nothing typical about the versatility and usefulness of pallet racks. In fact, this might just be the most adaptable materials handling system, offering both standard and customisable solutions.
Standard solutions refer to the most commonly used types of racking, which generally include floor stacking, selective pallet racking, drive-in or drive-through systems, as well as pallet flow racks. Some warehouse managers and specialists in the field would also include push back racking systems in this category, mainly because they’ve become quite popular lately. The push back racks can be fabricated in both roll and structural form. The roll formed racks are made of columns supported by beams, while the structural ones feature beams that are bolted.
Push back racking is perfect for bulk storage, as these systems usually run multiple levels high. They also got double deep racking configuration, or even multiple deep, which means the systems have the capacity to store products running 2 or more pallets deep. When loading a pallet onto the structure, this last one pushed back the one that rests on the rails, thus featuring a Last In First Out loading system. Structurally speaking, push back racking systems make use of sliding carts and inclined rails and they are, most of the times, constructed with double lanes.
Mobile Pallet Racking for Maximum Storage Density
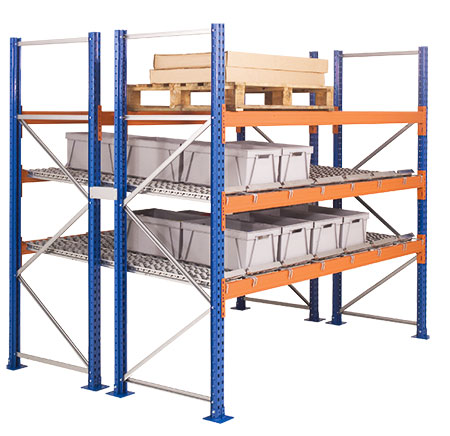
While there are many standard solutions that can offer high density storage, such as drive in racking or flow racks, many warehouses and storage facilities need even more, a bespoke solution that can offer them maximum storage density without compromising product access. Mobile pallet racking is that solution, having the ability to double the storage capacity of standard structures. The benefits of this type of system come from its ability to better utilise the existing storage space and include not only extremely efficient use of floor space, but also computer or electronically controlled storage and reduction in costs.
The basic configuration of mobile pallet racking features racking units that are mounted on powered moving bases, which means there’s no need for multiple aisles any more. These units can carry very heavy loads and run up to considerable heights, therefore providing maximum storage density. Although these systems are great for use in warehouses, their optimal use of temperature-controlled areas and operational safety at -30 ° C make them ideal for cold stores, whether you’re storing frozen or refrigerated goods.
Mobile pallet racking systems can have a modular design, which means they can be adapted to the particularities of your existing space and your needs. They can also be designed for narrow aisle racking, as well as wide aisle forklift truck circumstances.
Pallet Live Racking for Great Flow of Products
If you’re after high density storage but don’t want to block stack your pallets as to maintain a good flow of products, then pallet live racking or live storage is the ideal solution for you. This type of racking works with a loading front and an off-loading front, which leads to a First In First Out (FIFO) scenario. At the loading front, pallets are loaded onto roller lanes, which are basically dedicated lanes of inclined gravity rollers set at an established gradient. These pallets, when a load is picked, roll to the off-loading front, thus providing a good stock rotation. Some systems can even regulate the movement of pallets through brakes and speed controls, therefore making stock rotation automatic. As a result, only very few forklift truck movements are required to manage the flow of goods, meaning that most types of trucks can be used.
For the food industry, which works with perishable goods, but also other environments where products need to be rotated frequently, there is no better option than pallet live racking. The system is quite similar to push back racking, but instead of a LIFO operation it conducts a FIFO stock rotation. Pallet live racking suits not only goods with expiration dates, but also storage facilities with small numbers of SKUs, but in a high quantity of pallets. It’s also recommendable for fast-moving products and environments where items must be retrieved quickly.
Carton Flow Racking for Hand Loadings
Carton live racking, or flow racking, operates in a similar way to pallet live racking, but it is designed for goods that are picked and loaded by hand. However, the MO is very much alike, with roller tracks angled at a small gradient and the lower side set at the off-loading front. Because the products are loaded at the higher end and then they roll down gently, by the force of gravity, as each item is removed from the off-loading face, the carton flow racking system creates a FIFO operation as well.
The main benefits of carton live racking are the increased speed of order preparation and the fact that intervention in stock replenishment is no longer needed. Both benefits lead to enhanced picking performance, which can be further increased if you choose to incorporate WMS software. The best suitable environments for carton flow racking are storage facilities that register large picking volumes, because they enable increased quantities of immediately accessible goods, while at the same time minimising the distance travelled by pickers.
Carton live racking usually requires wide aisles, but it can be adapted to several other configurations as well, depending on the layout of the storage facility. Apart from providing automatic stock replenishment and reducing order preparation time, the carton flow racking system also gives the perfect turnover, allowing for a higher number of SKUs at the front of the structure.
Shuttle Racking for Staffing Limitations
Similar to drive in racking, pallet shuttle systems are semi-automated storage solutions. They are perfect for warehouses and storage facilities where human resources are limited because the shuttle does a great proportion of the work. The shuttle loads and unloads goods, handling goods inside channels, which means there is no need for forklift trucks, so this type of racking is not effective only from a human resources point of view, but also from a costs and time point of view.
Shuttles are remote-controlled and shuttle racking is ideal for warehouses that store a great number of pallets per SKU. Due to the fact that the FLT travel distance is significantly reduced, retrieval times are far more efficient with this type of racking, not to mention that it comes with the added benefit of allowing both FIFO and LIFO operations. The system enables high density storage, because pallets can be stacked deeper with this shuttle structure than any other type of racking, leading to a maximisation of warehouse space. However, product accessibility is not compromised, because the shuttle enables individual access to each and every tunnel.
As the shuttle transports goods back and forth and even loads the lanes, operators and warehouse workers can focus on other activities and task, which increases productivity and handling capacity. Moreover, as there is no manual handling of pallets, the risk of goods damage within shuttle racking is greatly minimised.
Best Racking System for Your Warehouse
When it comes to space-saving solutions for your warehouse, it’s not just the type of pallet racking that’s important, but also the way you use it, the way you adapt it to the layout and configuration of your space. There are certain distinguishing characteristics that you should take into account and compare when looking into different pallet racking systems, such as individual pallet access, floor or volume utilisation and whether or not FIFO can be obtained. Some options are the best at handling mixed items, while others provide better floor optimisation.
Narrow Aisle Racking is the best option if you need a system that provides good individual pallet access. It’s also the systems that’ll require the lowest investment in racks, but it’s not the best option as far as floor utilisation goes, where drive-in racking systems do a much better job. However, due to the fact that narrow aisle racking systems require the use of special trucks, which lift higher and work faster than then the general purpose trucks, speed and productivity increase.
Double Deep Racking is the ideal system if what you’re looking for is to increase storage capacity and you don’t mind the investment of special trucks, which are required for pallet handling. Double deep racking systems can increase pallet storage by up to 15%, but they can only be accessed from one aisle. Nevertheless, this system is very well suited for high turnover stock, enabling you to maintain good selectivity.
Drive In Racking is the best option for both high floor utilisation and high volume utilisation, featuring one entry/exit way. This system offers high density storage and operates on a LIFO basis. It’s ideal for low turnover products, where there are many pallets per SKU. Drive in racking is also suitable for cold storage, as well as for rack-clad buildings, enabling you to manage retrieval times and minimise damage to pallets.
Depending on the type of stock you have and the priority of your warehouse operations, a certain pallet racking system may suit you a lot better than the other, which is why comparing these distinguishing characteristics is important. Installing a narrow aisle racking in a warehouse where you have high volumes of pallets per SKU can be as disastrous as installing double deep racking where you need speedy retrieval or where you store perishable goods that need a FIFO operation.
Browse our storage designs
design
solutions
solutions
pallet
racking
racking
warehouse shelving
two
tier
tier
stockroom shelving
mobile
shelving
shelving
customised design
partitioning solutions